Gothic Reimagined
through the lens of ai
Design Team: Dustin White Design | Dustin White & Christopher Pope
Fabrication Team: Concr3de | Eric Geboers, Kostya Skrypnyk, Glenn Ton, Ion Martinez de Apellaniz
AI : Midjourney
A.I. to Stone
Translating a 2D generated image into 3D printed stone.
A.I. & Design
The rise of generated imagery
Gothic Reimagined is the first AI. generated image translated into 3D form and created physically in stone.
A.I.-generated media surged across the internet in 2022 as designers and artists collectively figured out the purpose of these disruptive tools. MidJourney, one of the more popular platforms focused on Text-to-Image generation, was the platform chosen for this particular project.
Dustin White, the founder of Dustin White Design and Director of Digital Design & Fabrication at NYIT, has been exploring the use of these tools as a form of rapid concept sketching. Developing the skill and craft of writing the prompts was paramount to creating a sense of refined communication and collaboration with the A.I. in the pursuit of producing more accurate and convincing images.
Dustin created a collection via. MidJourney titled “Gothic Reimagined”: a series of images visualizing Gothic Architectural styled details and compositions through the lens of A.I. As the power of this software currently exists in the 2D space, it was then our job as the design team to interpret these images into the 3D realm for further exploration. To us, this is the first step in discovering how a designer might utilize this media in a design process outside of concept sketching. With that said, because it was the first trial, there was an active decision made to interpret the images as directly as possible in order to preserve the character that emerged from the A.I.
Concr3de, a company specializing in 3D printing with powdered stone, created an opportunity to realize these images in physical material. The process and materials lend themselves to the existing conversation given that the existing context (Gothic Architecture) has a strong relationship with solid stone and analog procedures. Being able to translate this imagery through 3D printing and in a material not widely explored with this technology truly grounds this lens in the 21st century.
The following process was a fruitful collaboration between A.I., the designer, and the fabricator. The original four images were translated into two joined towers and finally presented at MARMOMAC 2022 in Verona, Italy.
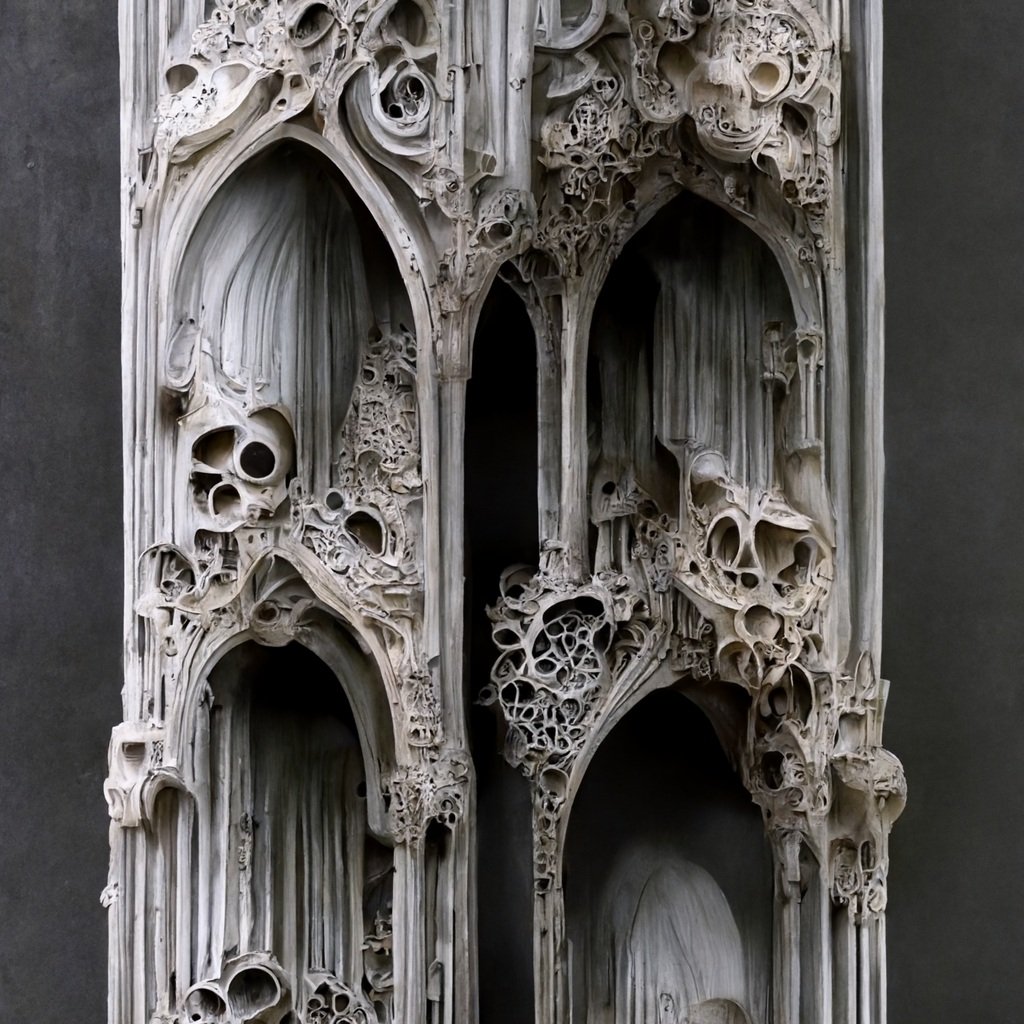
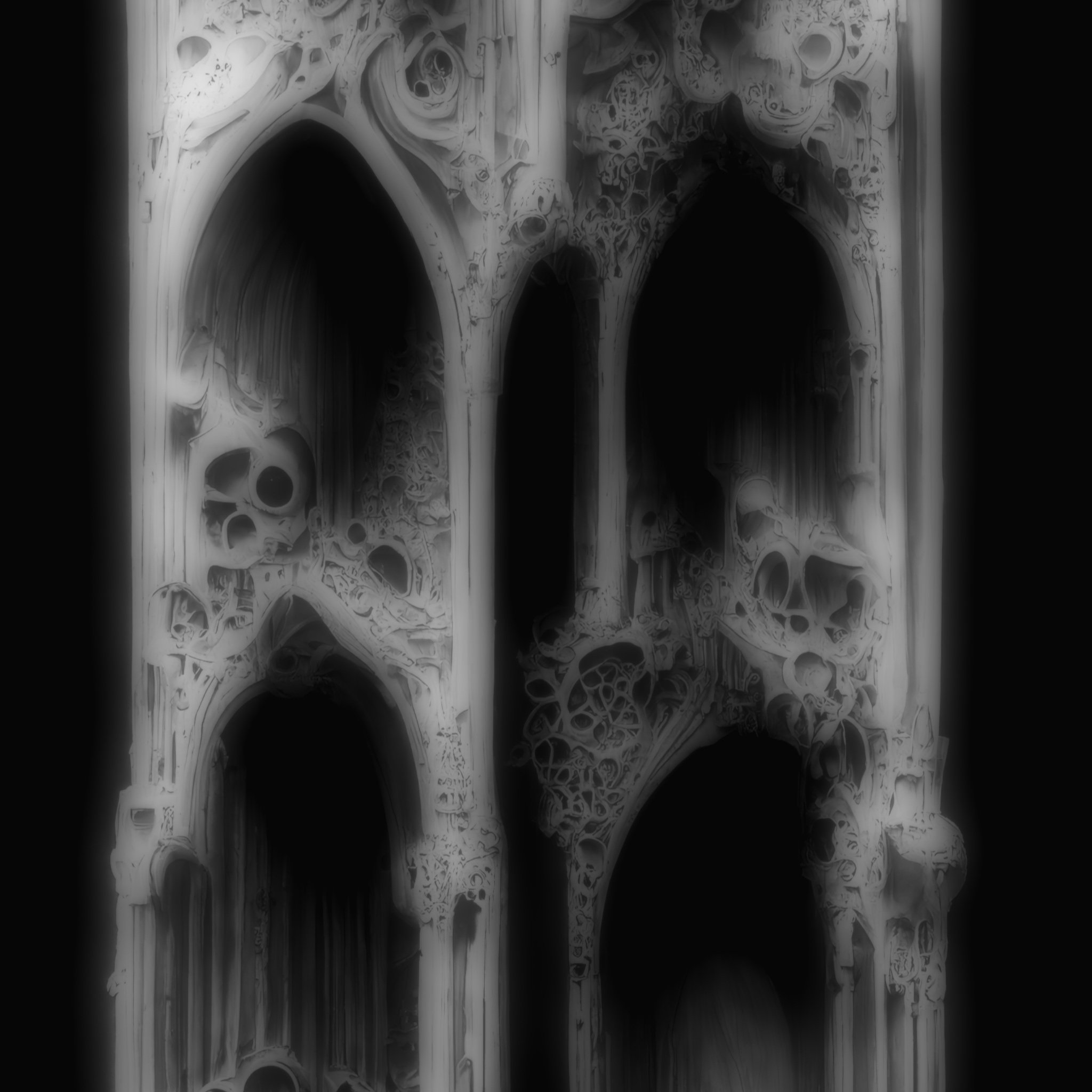
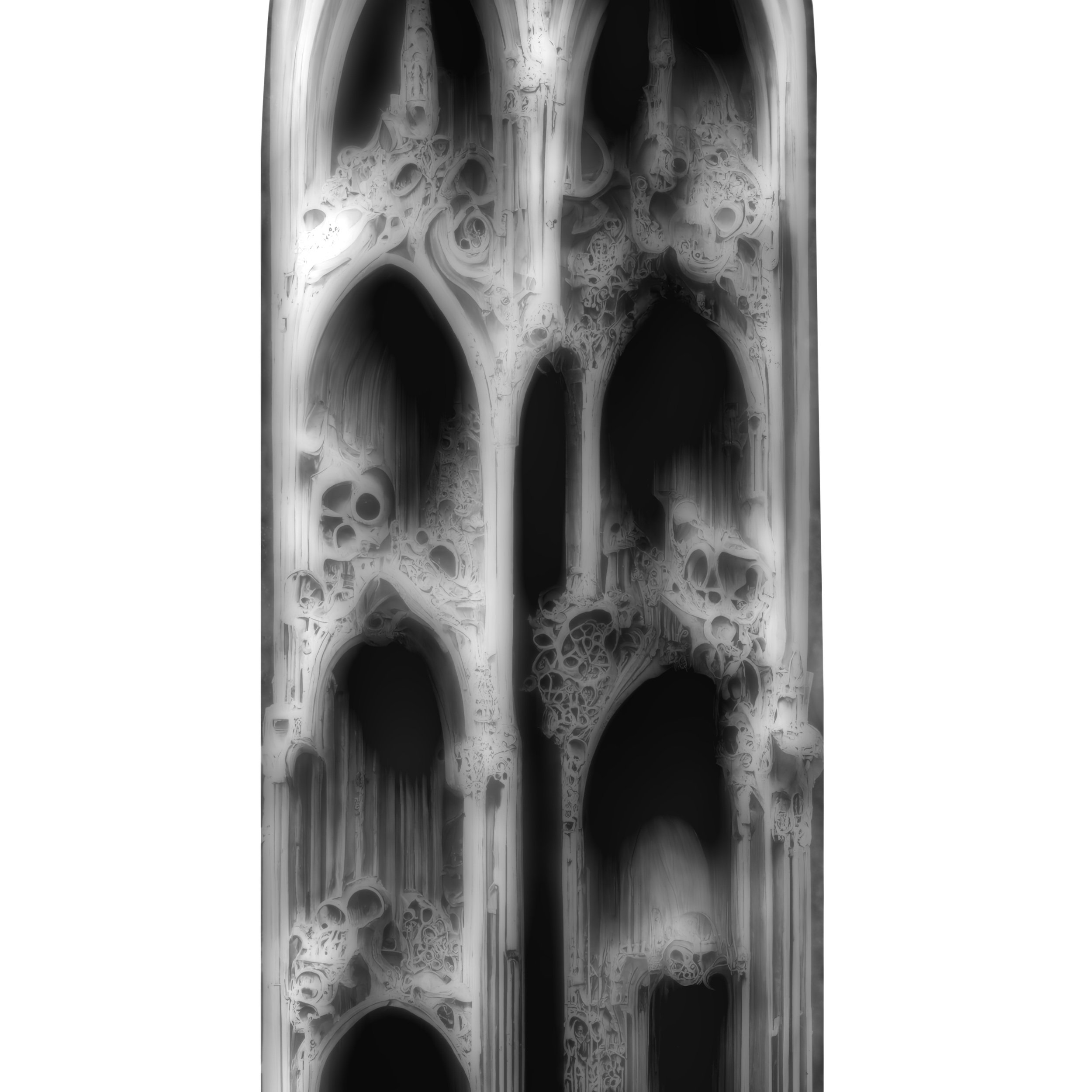
Translation
+ Interpretation
The decision to translate the imagery into 3D while preserving as much of the original detail as possible created some challenges. These images are generated with no such intent, dramatic lighting that fights against existing workflows for such 2D-to-3D translations, and some details can be quite “non-sensical”. As the process of trial and error began, our eyes quickly tuned to read depth and detail in ways our software could not so easily interpret. This required not only iterating through imagery to find which types of results worked best, but also tuning our latter processes to better assist in the translation without veering too far from that initial human interpretation. Depth and logic in our eyes are not always the same as that of the computer.
We learned throughout the process that some images translated much easier than others, some details more suited for reality and that even with the power of A.I. upscaling (inside and outside of MidJourney) resolution remained a limitation. There were many limitations of software, hardware, and human ability that impacted the entirety of the process but perhaps this plays into the beauty of the physical thing itself and fully exposes its novel state.
Fabrication
Negotiation
Being honest with the process without ignoring the original intent (translating vs interpreting) was tricky. While Concr3de develops machines that can print much larger constructs in a single piece, for our process we were limited to one of their smaller machines for in-house testing. This created two problems: 1) The image being translated must now be cut into pieces & 2) the stability of the final construct, especially between the two halves of the column, was now in question.
Each part was printed on average in 6 to 8 hours in completely solid powdered stone. Registration points were added between the seams to simplify alignment and a tongue-and-groove technique was used to secure each face of the towers to one another [animation to the left]. After some initial tests and simulation, the original models were reduced in volume without reducing the overall depth of the model to save on material and cut down on the already extreme weight of the finished sculptures [below]. In the end, two towers were produced from four images, averaging twenty parts per tower, and just over 400kg per tower (that’s around 900 lbs each). Concr3de printed each part and assembled them before shipping the final constructs to Verona, Italy for display at MARMOMAC 2022.
Record
the process
In collaboration with Bearr the process was documented and produced into the following video.